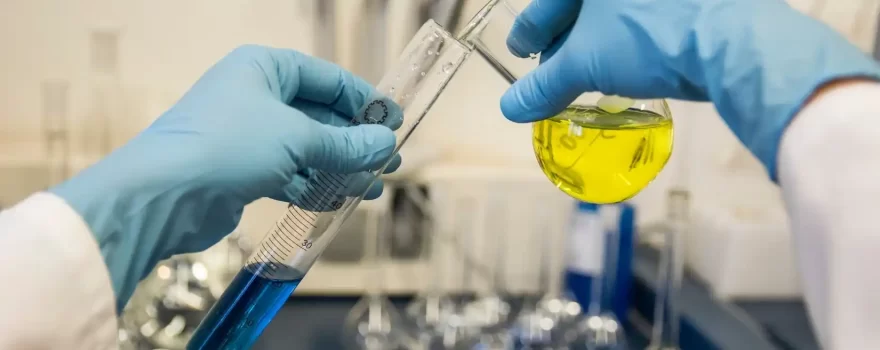
Table of Contents
Use Polyester resin textile chemicals are key to modern textile manufacturing, enhancing the performance and aesthetics of polyester fabrics. They improve properties like colorfastness, durability, and wrinkle resistance while offering stain, water, and fire resistance. These versatile chemicals support applications from casual wear to sportswear and industrial fabrics. With innovation, they continue to meet industry demands for sustainability and superior fabric performance.
Composition and Role in Textiles
Polyester resin is a synthetic polymer used in textiles to enhance the properties of polyester fabrics. Applied as a liquid and cured through heat or chemical reactions, it acts like a protective coating that modifies the fabric’s behavior.
For example, polyester resin can create a water-resistant barrier or stiffen the fabric, improving wrinkle resistance and stability. Depending on its composition, the resin may penetrate fibers or form a surface film, tailoring the fabric’s performance to specific needs.
Use Polyester Resin Textile Chemicals: Applications and Benefits
- Improved Durability: Polyester resin boosts fabric strength, enhancing resistance to abrasion, tearing, and pilling, which extends product lifespan.
- Enhanced Aesthetics: It provides a smoother texture, uniform appearance, and vibrant, long-lasting colors.
- Enhanced Functionality: Polyester resin imparts valuable properties like water repellency, stain resistance, wrinkle resistance, and flame retardancy.
- Cost-Effectiveness: Despite initial costs, improved fabric longevity and reduced replacements lower overall expenses.
Types of Polyester Resins in Textile Manufacturing
- Unsaturated Polyester Resins: Known for versatility and ease of use, these are widely applied for fabric stiffening, crease resistance, and water repellency.
- Saturated Polyester Resins: Ideal for applications demanding high chemical resistance and durability, they are commonly used in industrial fabrics and protective clothing.
- Vinyl Ester Resins: Offering superior chemical resistance and mechanical strength, these are perfect for high-performance textiles like marine fabrics and protective gear.
The choice of resin depends on the application’s requirements, including desired properties, budget, and processing conditions.
Applications of Polyester Resin in Textiles
- Fabric Stiffening and Shaping:
- Shirt Collars and Cuffs: Adds crispness and durability to structured components.
- Shape Retention: Maintains the form of garments like suits and dresses.
- Wrinkle Resistance:
- Ideal for easy-care fabrics, reducing ironing needs and enhancing convenience.
- Water and Stain Repellency:
- Perfect for outdoor wear, upholstery, and industrial fabrics, offering protection from water and stains.
- Flame Retardancy:
- Used in protective clothing for hazardous environments, enhancing safety.
- Surface Modification:
- Improves smoothness and softness, providing a comfortable feel against the skin.
- Special Effects:
- Creates textured fabrics with unique patterns and visual appeal.
These diverse applications highlight polyester resin’s critical role in enhancing fabric performance and aesthetics, tailored to the specific needs of modern textile manufacturing.
Polyester Resin in Fabric Coating and Protection
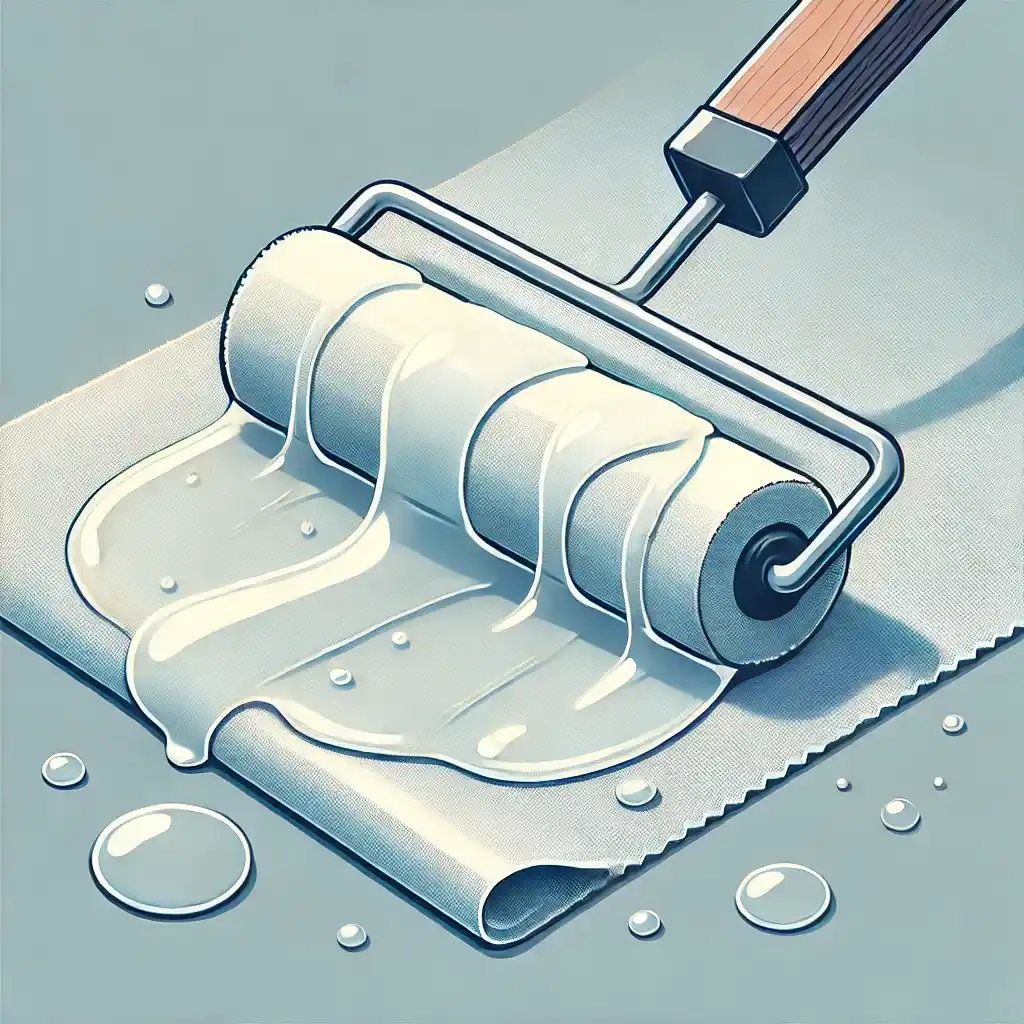
Polyester resin is a cornerstone of fabric coating and protection, delivering durability and enhanced performance for textiles across industries.
How Polyester Resin Protects Fabrics
- Protective Barrier: Forms a coating that shields fibers from moisture, abrasion, and chemicals.
- Enhanced Durability: Extends fabric lifespan by improving resistance to wear and tear.
- Functional Properties: Imparts water repellency, stain resistance, and flame retardancy.
Key Applications
- Outdoor Fabrics: Tents, tarpaulins, and furniture covers gain resistance to rain, UV rays, and mildew.
- Industrial Fabrics: Coatings enhance durability and chemical resistance for fabrics in construction and agriculture.
- Protective Clothing: Adds fire resistance and chemical protection for hazardous environments.
- Upholstery: Protects against stains, wear, and tear, making fabrics more durable and easy to clean.
Benefits of Polyester Resin Coatings
- Durability: Superior resistance to abrasion and tearing.
- Chemical Resistance: Shields fabrics from harsh chemicals and solvents.
- Weather Resistance: Protects against rain, UV rays, and environmental damage.
- Versatility: Customizable for water repellency, stain resistance, and flame retardancy.
- Cost-Effectiveness: Extends fabric lifespan, reducing replacement costs.
By forming a robust protective layer, polyester resin ensures fabrics perform better and last longer, making it indispensable in textile innovation.
Polyester Resin’s Impact on Fabric Strength and Flexibility
Increased Strength
- Stiffening: Polyester resin enhances resistance to bending and tearing, adding rigidity and structural support, especially in applications like collars and cuffs.
- Reinforcement: Acts as a binding agent, strengthening fabric fibers and boosting tensile strength and abrasion resistance.
Potential for Reduced Flexibility
- Stiffening Effect: While beneficial for structured fabrics, stiffening can decrease comfort and limit suitability for garments requiring high mobility.
- Resin Build-up: Over-application may result in a rigid, board-like texture, reducing drapability and softness.
Balancing Strength and Flexibility
- Resin Selection: Opt for flexible resin formulations to maintain softness while adding strength.
- Optimized Application: Adjust resin content to achieve the desired performance without compromising comfort or flexibility.
Key Considerations
The impact of polyester resin depends on fabric type, resin formulation, and application method. Careful planning ensures the right balance of strength and flexibility, tailored to the specific needs of the fabric.
Polyester Resin in Composite Textile Fabrics
Polyester resin is essential in creating composite textile fabrics, turning them into high-performance materials with enhanced strength, stiffness, and durability.
How Polyester Resin Works in Composites
- Binding Agent: Acts as a glue, holding together reinforcing fibers like glass, carbon, or aramid.
- Matrix Phase: Forms the continuous phase, encapsulating and supporting the fibers.
- Property Enhancement: Combines resin and fibers for superior mechanical properties beyond individual components.
Key Applications
- Fiberglass Reinforced Plastics (FRP):
- Marine: Boats, yachts, and marine structures.
- Construction: Roofing and building components.
- Automotive: Lightweight body panels and spoilers.
- Sports Equipment: Surfboards and kayaks.
- Industrial Fabrics:
- Protective Clothing: Fire-resistant and chemical-protective suits.
- Conveyor Belts: Reinforced for heavy-duty applications.
- Geotextiles: Used in soil stabilization and erosion control.
Benefits of Polyester Resin in Composite Textiles

- Cost-Effectiveness: Affordable compared to alternatives like epoxy.
- Ease of Processing: Cures easily at low temperatures.
- Versatility: Customizable for strength, chemical resistance, and flame retardancy.
- Mechanical Excellence: High strength-to-weight ratio and impact resistance.
Challenges and Considerations
- Temperature Resistance: Limited compared to epoxy composites.
- Chemical Resistance: May not withstand certain environments.
- Environmental Concerns: Some formulations contain VOCs, impacting sustainability.
Despite these challenges, polyester resin remains a cost-effective and adaptable material, enabling a wide range of innovative applications in composite textiles.
Environmental Considerations of Polyester Resin Use in Textiles
Polyester resin offers significant benefits for textile manufacturing, but it also raises notable environmental concerns.
Key Environmental Challenges
- Production and Manufacturing:
- Fossil Fuel Dependence: Derived from petroleum, polyester production contributes to greenhouse gas emissions.
- Energy Intensive: Requires substantial energy, often sourced from fossil fuels, increasing carbon emissions.
- Chemical Use: Involves potentially harmful chemicals that must be carefully managed to avoid environmental harm.
- Microplastic Pollution:
- Shedding Microfibers: Washing polyester garments releases microplastics into waterways, harming aquatic ecosystems.
- Environmental Persistence: Microplastics degrade slowly, accumulating in the food chain and ecosystems.
- Waste and Disposal:
- Landfill Accumulation: Polyester products persist for centuries in landfills, contributing to long-term pollution.
- Limited Recycling: Recycling processes are underdeveloped, and recycled polyester often has lower quality than virgin material.
Strategies to Mitigate Environmental Impacts
- Sustainable Production:
- Shift to renewable energy sources to lower carbon emissions during manufacturing.
- Closed-Loop Recycling:
- Develop and promote recycling systems to reduce waste and reliance on virgin polyester.
- Minimizing Microplastic Release:
- Wash garments less frequently, use cold water, and install washing machine filters to capture microfibers.
- Bio-Based Alternatives:
- Invest in research for bio-based polyester alternatives to reduce dependence on fossil fuels.
Moving Forward
Acknowledging these challenges is vital for fostering sustainability in textile manufacturing. By adopting eco-friendly practices and exploring innovative solutions, the industry can reduce the environmental impact of polyester resin and work toward a more sustainable future.
Polyester Resin in Textile Finishing: A Detailed Overview
Polyester resins are integral to textile finishing, offering enhancements in performance, durability, and aesthetics. They modify the fabric’s surface and internal structure, imparting key properties like wrinkle resistance, water repellency, and flame retardancy.
Key Finishing Processes Involving Polyester Resins
- Wrinkle Resistance Finishing
- Mechanism: Resins crosslink with fabric fibers, forming a network that reduces fiber movement and prevents wrinkles.
- Benefits: Improved wrinkle recovery, reduced ironing, enhanced durability.
- Common Resins: Dimethyloldihydroxyethyleneurea (DMDHEU), melamine-formaldehyde resins.
- Water and Stain Repellency Finishing
- Mechanism: Creates a hydrophobic barrier on the fabric surface.
- Benefits: Protects against stains, enhances durability, and improves wet-condition performance.
- Common Resins: Fluorocarbon-based and silicone resins.
- Flame Retardant Finishing
- Mechanism: Combines with flame retardants to inhibit combustion.
- Benefits: Improves fire resistance for protective clothing and upholstery.
- Common Resins: Phosphorus-containing and halogenated resins.
- Stiffening and Shaping Finishing
- Mechanism: Provides structure and shape retention, especially in garments like collars and cuffs.
- Benefits: Enhances garment appearance and drape.
- Anti-Pilling Finishing
- Mechanism: Forms a protective film on the fabric surface to reduce pilling.
- Benefits: Extends lifespan and maintains fabric appearance.
Advantages of Polyester Resin Finishing
- Improved Performance: Adds wrinkle resistance, water repellency, and flame retardancy.
- Increased Durability: Enhances resistance to wear, pilling, and abrasion.
- Enhanced Aesthetics: Improves drape, hand feel, and overall fabric appearance.
- Versatility: Applicable to apparel, home furnishings, and industrial textiles.
Challenges and Considerations
- Environmental Impact: Some resins release volatile organic compounds (VOCs).
- Health Concerns: Certain finishes may cause allergic reactions.
- Fabric Hand Impact: Overuse can make fabrics stiff or uncomfortable.
Challenges and Limitations of Polyester Resin in Textiles
While polyester resins provide numerous advantages in textiles, they come with challenges and limitations that require careful management.
1. Environmental Concerns
- Microplastic Pollution: Washing polyester garments releases microplastics, harming aquatic ecosystems.
- Volatile Organic Compounds (VOCs): Processing can emit VOCs, contributing to air pollution.
- Non-renewable Resources: Polyester production relies on petroleum, exacerbating climate change and environmental degradation.
2. Health and Safety
- Skin Irritation: Some formulations may cause irritation or allergic reactions.
- Respiratory Issues: Resin fumes during processing can irritate the respiratory system.
- Flammability: Polyester is inherently flammable, requiring additional flame-retardant treatments.
3. Performance Limitations
- Temperature Resistance: Limited compared to materials like ceramics or high-performance polymers.
- Chemical Resistance: Vulnerable to degradation by specific chemicals and solvents.
- Dyeing Challenges: Requires specialized dyes and processes for effective coloring.
4. Processing Limitations
- Curing Time: Can slow down production due to time-intensive curing.
- Uniformity: Achieving consistent resin distribution and curing is challenging.
- Waste Generation: Production and application processes generate waste requiring proper management.
5. Cost Considerations
- Raw Material Costs: Polyester resin prices vary with formulation and market dynamics.
- Processing Costs: Specialized equipment and expertise increase overall production costs.
6. Impact on Fabric Hand
- Stiffness: Excess resin can reduce flexibility and drapability, affecting comfort and usability.
Mitigation Strategies
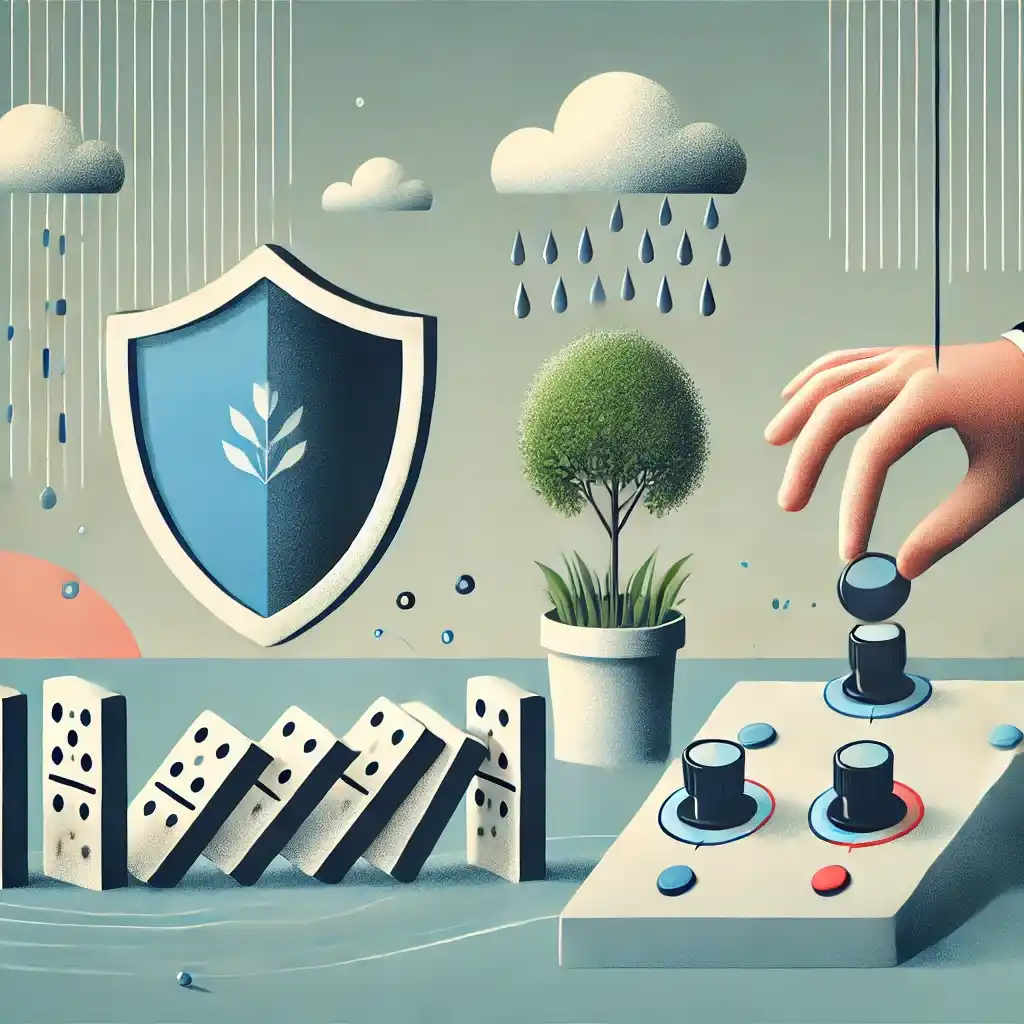
- Sustainable Production: Adopt renewable energy and bio-based raw materials.
- Improved Recycling: Develop closed-loop systems for polyester textiles.
- Eco-Friendly Resins: Invest in research to create non-toxic, biodegradable resin alternatives.
- Safety Measures: Implement stringent controls to reduce exposure to harmful fumes and chemicals.
- Optimized Application: Balance resin usage to enhance properties without compromising comfort.
Advancements in Polyester Resin Applications for Textiles
- Sustainable Resins:
- Bio-based resins reduce fossil fuel reliance.
- Recycled resins promote a circular economy.
- Nanotechnology:
- Nanofillers enhance strength and conductivity.
- Nanostructured resins improve durability and resistance.
- Smart Textiles:
- Integrates sensors for “smart” fabrics.
- Self-healing resins extend product lifespan.
- 3D Printing:
- Enables customized and intricate designs.
- Speeds up prototyping and production.
- Advanced Processing:
- Plasma treatment enhances resin adhesion.
- Nanoimprinting adds functionality and aesthetics.
These innovations drive sustainable, high-performance, and multifunctional textiles for modern needs.
How to Choose the Right Polyester Resin for Textile Products
Step | Details |
1. Define Desired Properties | |
Fabric Type | Identify the base material (e.g., cotton, polyester, nylon). |
End Use | Specify the application (e.g., clothing, upholstery, industrial fabrics). |
Required Properties | Strength and durability Stiffness (e.g., collars, cuffs) Flexibility for comfort Functional properties (e.g., water repellency, flame retardancy) Aesthetic qualities (e.g., hand feel, appearance). |
2. Consider Resin Types | |
Unsaturated Resins | Versatile; ideal for stiffening, crease resistance, and water repellency. |
Saturated Resins | High chemical resistance and durability; suitable for industrial fabrics and protective clothing. |
Vinyl Ester Resins | Superior chemical and mechanical properties for high-performance applications. |
Specialty Resins | Tailored for specific needs like flame retardancy, antimicrobial properties, or UV resistance. |
3. Evaluate Resin Properties | |
Viscosity | Determines application and penetration into the fabric. |
Curing Characteristics | Time, temperature, and curing requirements. |
Flexibility | Assess the resin’s impact on comfort and hand feel. |
Environmental Impact | Evaluate VOC emissions and potential for microplastic release. |
4. Consult with Resin Suppliers | |
Technical Data Sheets | Review performance details of resin options. |
Technical Support | Seek expert recommendations tailored to your needs. |
Sample Testing | Test resin samples on a small scale for suitability. |
5. Pilot Testing | |
Conduct Trials | Perform small-scale trials to evaluate performance. |
Evaluate Results | Check for desired properties (e.g., strength, repellency, flexibility). |
6. Optimize Application | |
Application Methods | Experiment with padding, spraying, or dipping to ensure uniform application. |
Resin Concentration | Fine-tune resin concentration to achieve desired properties without compromising fabric hand feel or comfort. |
Resin Concentration Fine-tune resin concentration to achieve desired properties without compromising fabric hand feel or comfort.
The future of polyester resin in textile chemistry hinges on balancing its benefits with environmental and social responsibility.
Key Trends:
- Sustainability: Shift toward renewable resources and circular economy practices.
- Innovation: Development of eco-friendly, high-performance resin formulations.
- Collaboration: Partnerships among researchers, manufacturers, and consumers to tackle challenges and seize opportunities.
Looking Ahead:
Polyester resin will remain crucial in textiles, thriving through sustainable practices, innovative solutions, and responsible consumption to ensure a greener future.
Read more: Use Hydrogen Peroxide in Textile Chemicals