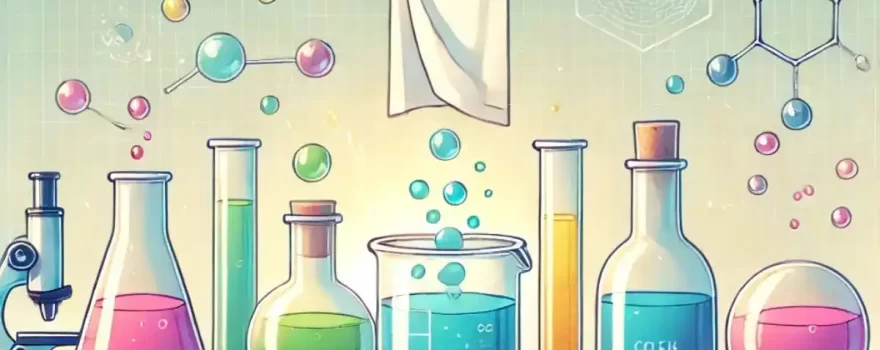
The Formulation of Textile Chemicals Flowchart is vital for the textile industry. Textile chemicals transform raw materials into functional fabrics, impacting durability, comfort, and aesthetics. Effective formulation requires understanding chemical interactions, fabric properties, and end-use to optimize performance, minimize environmental impact, and meet consumer demands.
Table of Contents
Overview of Textile Chemical Formulation: Key Processes in Textile Chemical Formulation for Effective Processing
Process | Description | Key Considerations |
Needs Assessment and Target Definition | Clearly define specific requirements and desired outcomes for the textile chemical. | – Type of fabric – Intended application (e.g., dyeing, finishing, printing) – Desired performance (e.g., colorfastness, water repellency) |
Ingredient Selection and Sourcing | Select appropriate raw materials based on functionality, compatibility, and environmental impact. | – Synthetic vs. natural-based chemicals – Cost and availability – Regulatory compliance |
Formulation Development and Optimization | Experiment with ingredient combinations and parameters to achieve desired performance through laboratory trials. | Experiment with ingredient combinations and parameters to achieve desired performance through laboratory trials. |
Scale-up and Production | Transition laboratory formulations to production scales while maintaining consistency and quality. | – Quality control across batches – Robust production protocols |
Performance Evaluation and Testing | Rigorously test the final product to ensure it meets defined requirements and gather feedback for improvement. | – Colorfastness and durability – Environmental impact – End-user feedback |
By following these structured processes, the formulation of textile chemicals ensures effective processing, meets market demands, minimizes environmental impact, and guarantees safety and performance.
Raw Material Selection: Choosing the Right Raw Materials for Textile Chemical Development
Choosing the right raw materials is a critical step in the Formulation of Textile Chemicals Flowchart. The performance and sustainability of the final product heavily rely on the quality and characteristics of the ingredients used.
Category | Key Considerations |
Performance | – Select materials with desired functional properties (e.g., dyeing ability, wetting, dispersing). – Ensure compatibility with other formulation ingredients. – Assess impact on final fabric properties |
Sustainability | – Use renewable and biodegradable materials when possible. – Avoid hazardous chemicals, opting for safer alternatives. – Evaluate environmental impact during sourcing and production. |
Economic | – Prioritize cost-effective raw materials. – Ensure availability and mitigate risks of price fluctuations. – Partner with reliable and ethical suppliers. |
Regulatory Compliance | – Adhere to relevant environmental and safety regulations. – Stay updated on industry standards and best practices. |
By addressing these considerations, the selection of raw materials ensures optimal performance, compliance, and sustainability in the development of textile chemicals.
Step-by-Step Textile Chemical Formulation: A Detailed Breakdown
The Formulation of Textile Chemicals Flowchart is a systematic approach that guides us through the intricate process of developing effective and sustainable textile chemicals. Let’s break down the key steps involved:
By meticulously following these steps and utilizing the Formulation of Textile Chemicals Flowchart, we can develop innovative and sustainable textile chemicals that meet the evolving needs of the industry while minimizing environmental impact.
Step | Details | Key Considerations |
1. Needs Assessment and Target Definition | – Define the application (dyeing, printing, finishing). – Identify the fabric type (cotton, polyester, blends). – Set desired performance characteristics (e.g., colorfastness, durability, comfort). | – Environmental compliance. – Regulatory adherence. |
2. Ingredient Selection and Sourcing | – Evaluate synthetic and natural chemicals. – Prioritize renewable, biodegradable options. – Select reliable suppliers. | – Cost-effectiveness. – Availability. – Environmental impact. |
3. Formulation Development and Optimization | – Create initial formulations. – Perform laboratory-scale trials. – Use statistical methods for optimization. | – Ingredient compatibility. – Minimized trial numbers. – Performance consistency. |
4. Scale-Up and Production | – Conduct pilot production. – Ensure consistent quality with robust quality control measures. – Optimize production processes. | – Maintain product specifications. – Monitor costs and efficiency. |
5. Performance Evaluation and Testing | – Perform rigorous testing for colorfastness, durability, and special functions. – Gather end-user feedback. | – Continuous improvement. – Alignment with market and customer needs. |
Preliminary Testing and Adjustments: Ensuring Chemical Compatibility
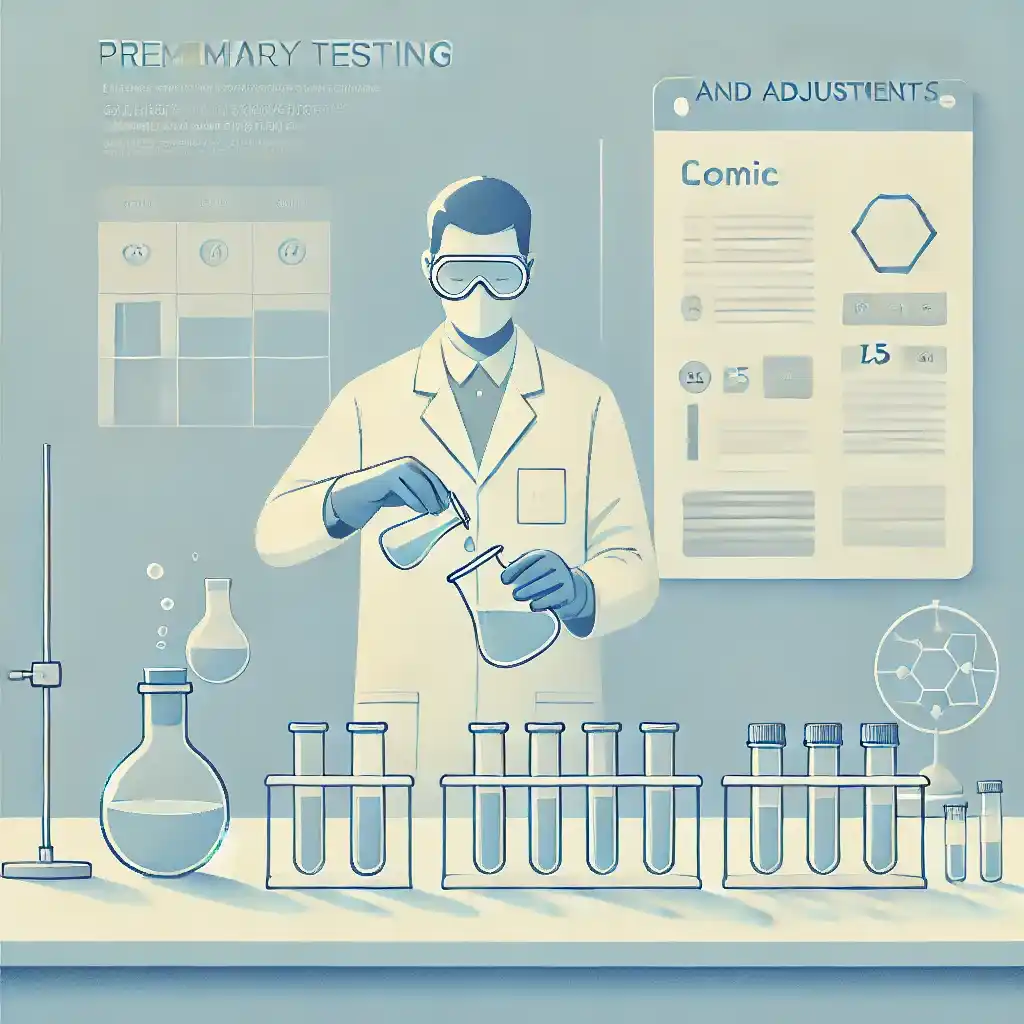
Key Aspects of Preliminary Testing:
- Compatibility Testing:
- Check chemical interactions: precipitation, color changes, gas evolution.
- Assess fabric compatibility: dye uptake, fabric damage, residual chemicals.
- Performance Evaluation:
- Conduct small-scale trials for:
- Colorfastness: Resistance to washing and light.
- Durability: Performance after repeated washing/dry cleaning.
- Sensory Properties: Hand feel, drape, and texture.
- Conduct small-scale trials for:
- Stability Testing:
- Evaluate storage stability under varying conditions (temperature, humidity).
- Determine shelf life for safety and effectiveness.
Adjustments:
- Modify ingredients to address compatibility or performance issues.
- Optimize processing parameters (e.g., temperature, time, pH).
- Add auxiliary agents for improved stability and efficacy.
- This ensures textile chemicals are effective, safe, and aligned with desired performance goals.
Pilot Batch Testing: Optimizing Textile Chemical Formulations
Pilot batch testing is a crucial step in the Formulation of Textile Chemicals Flowchart. It bridges the gap between small-scale laboratory trials and full-scale production, allowing us to:
Key Aspect | Key Aspect | Purpose |
Validate Laboratory Findings | Confirm that formulations developed in the lab perform effectively on a larger scale. | Ensure scalability and performance consistency. |
Identify and Address Potential Issues | ||
– Scale-Up Challenges | Address issues like mixing, heating, and cooling at larger volumes. | Prevent inefficiencies and maintain quality. |
– Equipment Limitations | Identify and adapt to production equipment constraints. | Ensure compatibility between formulation and machinery. |
– Consistency Issues | Test the reproducibility of the formulation at scale. | Guarantee uniform product quality across batches. |
Scale-Up Considerations | ||
– Equipment Selection | Choose appropriate equipment for mixing, heating, and other steps based on formulation properties. | Ensure efficient and accurate processing. |
– Process Control | Implement robust controls for critical parameters like temperature and mixing. | Achieve consistent results in production. |
– Material Handling | Develop safe and efficient procedures for handling large volumes of chemicals. | Minimize risks and streamline workflow. |
Performance Evaluation | ||
– Thorough Testing | Conduct comprehensive tests for colorfastness, durability, sensory properties, and environmental impact. | Verify that the pilot batch meets quality standards. |
– Comparison with Lab Results | Compare pilot batch performance to laboratory outcomes. | Ensure alignment with initial expectations. |
Data Analysis and Optimization | ||
– Analyze Data | Collect and analyze data to identify areas for improvement. | Refine formulations and processes for better outcomes. |
– Process Optimization | Adjust formulations, parameters, or equipment to enhance performance and efficiency. | Resolve issues and achieve optimal results. |
– Document Findings | Record all insights and observations from the pilot testing phase. | Provide a reference for full-scale production and future use. |
Optimization Techniques: Refining Formulas for Desired Properties in Textile Processing
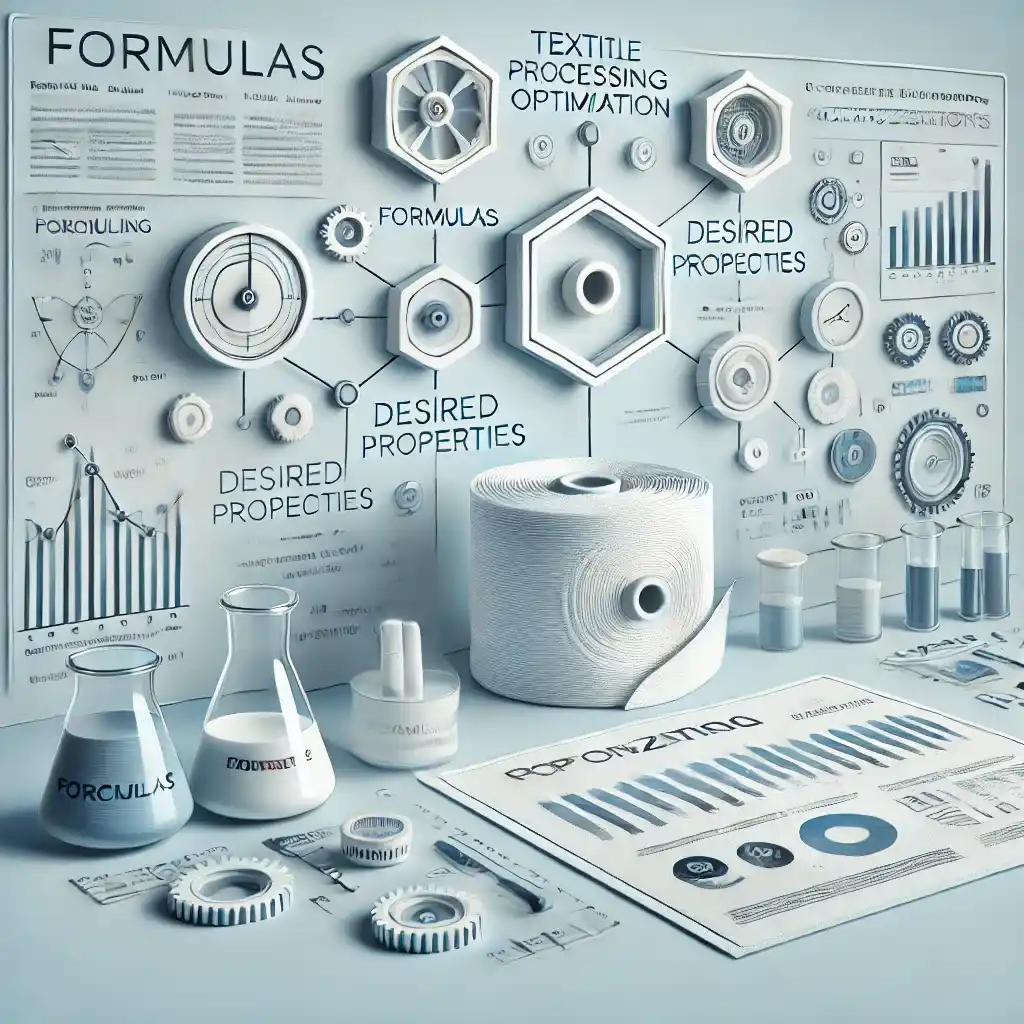
Key Optimization Techniques:
- Design of Experiments (DoE):
- Structured approach to test multiple variables (e.g., ingredients, parameters) efficiently.
- Minimizes experiments while maximizing insights.
- Statistical analysis identifies significant factors for optimal results.
- Response Surface Methodology (RSM):
- Develops mathematical models to link inputs (e.g., formulations, conditions) with outcomes (e.g., durability, colorfastness).
- Predicts optimal combinations of variables.
- Visualizes relationships through response surface plots.
- Artificial Intelligence (AI) and Machine Learning:
- Builds predictive models for formulation performance.
- Uses historical and experimental data for data-driven optimization.
- Continuously refines models for improved outcomes over time.
- Evolutionary Algorithms:
- Mimics natural selection to find the best solutions.
- Handles complex problems with multiple variables and constraints.
- Robust against noisy or uncertain data.
By leveraging these techniques, textile chemical formulations can be optimized for performance, cost-effectiveness, and sustainability.
Finalizing the Formulation: Production Scale Readiness
The final stage of the Formulation of Textile Chemicals Flowchart involves transitioning from successful pilot batches to full-scale production. This requires meticulous attention to detail and a robust quality control system.
Aspect | Details | Purpose |
1. Production Scale-Up | ||
– Equipment and Process Validation | Ensure production equipment and processes meet formulation specifications. | Guarantee consistent and reliable production. |
– Capacity Planning | Determine production capacity to meet market demand. | Avoid delays and shortages. |
– Raw Material Sourcing | Secure reliable and consistent sources of high-quality raw materials. | Maintain consistent input quality for production. |
2. Quality Control and Assurance | ||
– Comprehensive QC Plan | Implement quality checks at all stages: | |
– Incoming Raw Material Inspection | – Incoming Raw Material Inspection | Prevent defective inputs from affecting production. |
– In-Process Control | Monitor critical parameters (e.g., temperature, pH, mixing time). | Monitor critical parameters (e.g., temperature, pH, mixing time). |
– Finished Product Testing | Conduct thorough tests on finished products to meet standards. | Deliver high-quality, compliant products. |
Documentation | Record raw material usage, process parameters, and test results. | Ensure traceability and accountability. |
3. Safety and Environmental Compliance | ||
– Safety Protocols | Implement measures to protect workers from chemical hazards. | Ensure workplace safety and minimize health risks. |
– Environmental Management | Apply waste reduction, recycling, and eco-friendly practices. | Reduce environmental footprint and promote sustainability. |
– Regulatory Compliance | Adhere to all relevant environmental and safety regulations. | Avoid legal issues and maintain ethical standards. |
4. Cost Optimization | ||
– Continuous Improvement | Monitor and refine production processes to enhance efficiency. | Reduce operational costs while maintaining quality. |
– Supply Chain Management | Optimize supply chain to minimize costs and ensure timely material delivery. | Ensure cost-effective and uninterrupted production. |
By carefully addressing these considerations, we can successfully transition the finalized textile chemical formulation to full-scale production, ensuring consistent quality, safety, and environmental sustainability.
Comprehensive Quality Control Measures in Textile Chemical Formulation
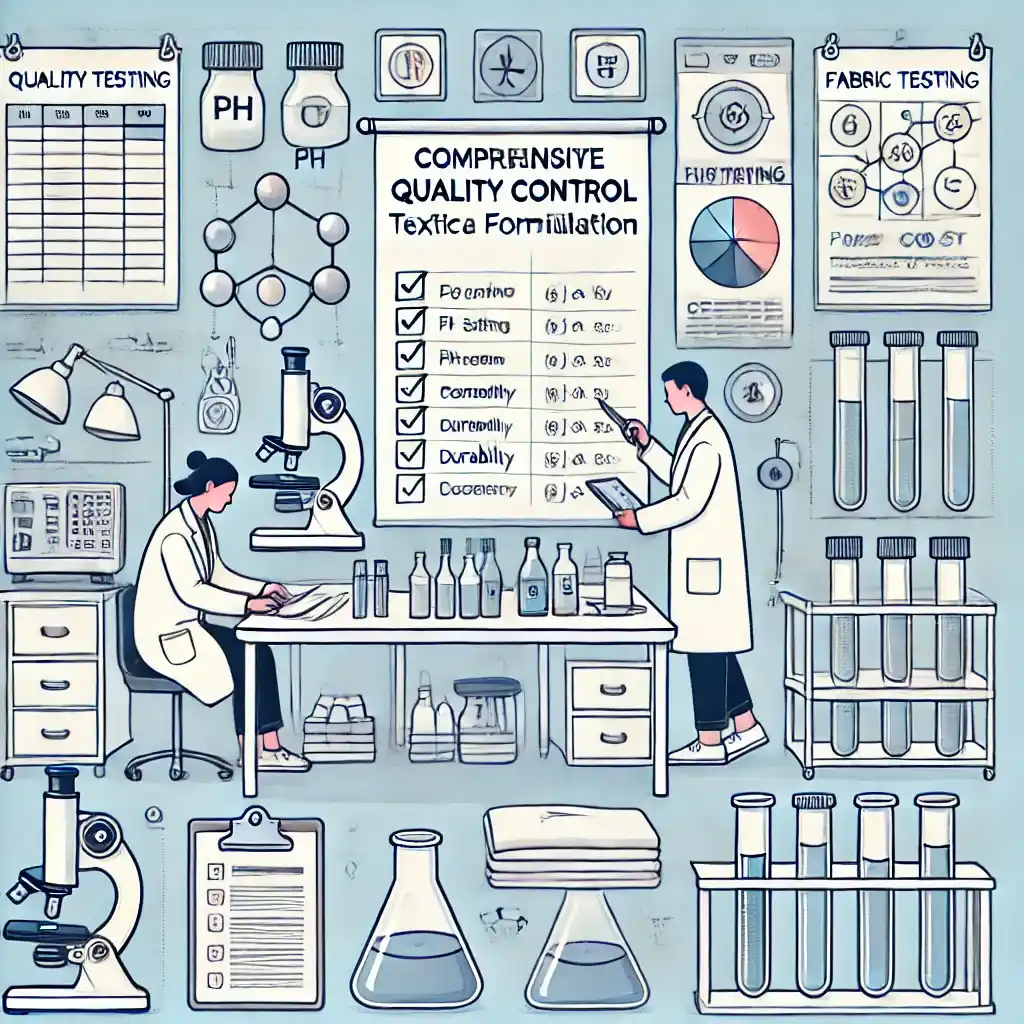
Ensuring quality control in textile chemical formulation is essential to guarantee consistent performance, safety, and adherence to standards throughout the production process. Below are key quality control practices restructured for clarity:
Raw Material Quality Checks
- Visual Inspection: Detect contamination, discoloration, or physical irregularities in raw materials.
- Chemical Verification: Conduct detailed tests to confirm material composition and purity:
- Titration: Measure concentrations of reactive substances like acids or bases.
- Spectrophotometry: Analyze the light absorbance of specific compounds.
- Chromatography: Separate and examine components in a mixture.
- Supplier Compliance: Periodically audit suppliers to verify adherence to quality and safety protocols.
Process Monitoring and In-Process Testing
- Critical Parameter Tracking: Continuously oversee essential factors such as:
- Temperature: Maintain precise control during heating, mixing, or cooling stages.
- pH Levels: Adjust pH to ensure reaction stability and effectiveness.
- Mixing Conditions: Verify uniformity through consistent mixing times and speeds.
- Sample Testing: Evaluate samples at intermediate stages for quality and consistency.
Finished Product Evaluation
- Performance Assessment: Verify the end product meets required specifications:
- Colorfastness: Test resistance to washing, light exposure, and wear.
- Durability: Check finishes like water repellency, flame retardancy, or wrinkle resistance.
- Fabric Properties: Assess the feel, drape, and tactile quality of treated materials.
- Chemical Safety Tests: Screen for harmful residues like heavy metals or hazardous substances.
- Stability Analysis: Store finished products under controlled conditions to observe long-term performance and safety.
Documentation and Standardization
- Detailed Record Maintenance: Document every step of the production process, including:
- Material specifications and test results.
- Production parameters and adjustments.
- Final product performance data.
- Quality Frameworks: Adhere to established standards like ISO 9001 to promote consistency and continuous quality improvement.
Commitment to Continuous Improvement
- Data Utilization: Regularly review quality control metrics to spot inefficiencies or trends.
- Issue Resolution: Investigate quality deviations using root cause analysis and implement corrective actions.
- System Upgrades: Periodically evaluate and enhance the overall quality management system to align with evolving standards and market needs.
By implementing these quality control measures, manufacturers can produce superior textile chemicals that are reliable, sustainable, and tailored to industry demands, while fostering innovation and compliance.
Impact of pH and Temperature on Textile Chemical Formulation and Performance
Factor | Impact | Key Considerations |
pH | ||
– Chemical Reactions | Influences ionization and reactivity of chemicals. | Maintain appropriate pH to ensure desired chemical interactions. |
– Dyeing | Affects dye uptake, colorfastness, and fabric appearance. | Adjust pH based on dye type and fabric requirements. |
– Finishing | Impacts the effectiveness of agents like softeners, wrinkle-release agents, and flame retardants. | Optimize pH for each finishing agent to achieve maximum performance. |
– Chemical Stability | Extreme pH values can degrade chemicals, cause precipitation, or lead to undesirable reactions. | Avoid overly acidic or alkaline conditions unless necessary for specific processes. |
– Fiber Compatibility | Specific fibers respond differently to acidic or alkaline conditions. | Match pH of processing bath to the fiber type (e.g., acidic for protein fibers, alkaline for cellulose). |
Temperature | ||
– Reaction Kinetics | Higher temperatures speed up reactions but can cause side reactions or chemical degradation. | Control temperature to balance reaction rates and prevent unwanted effects. |
– Dye Solubility | Increases solubility of dyes, improving uptake and penetration. | Increases solubility of dyes, improving uptake and penetration. |
– Fabric Properties | Impacts shrinkage, crease formation, and hand feel. | Maintain temperature within fabric tolerance levels to preserve quality. |
General Considerations | ||
– Optimal Ranges | Specific pH and temperature ranges vary for each chemical process and desired outcome. | Research and adhere to optimal conditions for each application. |
– Buffer Solutions | Stabilize pH during processing for consistent results. | Incorporate buffers in formulations where necessary. |
– Temperature Control | Accurate temperature management ensures reproducible outcomes and efficiency. | Use reliable temperature regulation systems during production. |
Controlling pH and temperature is crucial in textile chemical formulation to ensure optimal performance, efficient processing, and minimal environmental impact. These factors must be tailored to the specific requirements of each process and fabric type.
Environmental and Safety Considerations in Textile Chemical Formulation
Environmental Impact:
- Minimizing Pollution:
- Optimize processes to reduce waste and chemical usage.
- Implement water recycling and closed-loop systems.
- Control air emissions (e.g., VOCs) with effective pollution systems.
- Eco-Friendly Chemicals:
- Use renewable, biodegradable, and bio-based ingredients.
- Follow green chemistry principles (e.g., safer solvents, atom economy).
- Life Cycle Assessment:
- Evaluate environmental impact across the product lifecycle.
Safety Considerations:
- Chemical Safety:
- Assess hazards and enforce safe handling practices (e.g., PPE usage).
- Store chemicals securely to prevent spills and unauthorized access.
- Occupational Health:
- Train workers in chemical safety and emergency protocols.
- Ensure proper ventilation to reduce exposure to fumes and vapors.
- Prepare emergency response plans for spills or accidents.
Regulatory Compliance:
- Follow environmental regulations (e.g., wastewater, air emissions).
- Adhere to occupational health and product safety standards.
- Ensure finished products meet safety requirements (e.g., flammability, toxicity).
Integrating these measures ensures sustainable, safe, and effective textile chemical formulations.
Applications of Textile Chemicals in Fabric Processing
Preparatory Processes, Dyeing, and Printing
Textile chemicals are vital in the initial stages of fabric preparation, dyeing, and printing. These processes lay the foundation for achieving desired fabric properties, ensuring smooth transitions to later stages of production.
Process | Application | Details |
Preparatory Processes | ||
– Scouring and Washing | Removes natural impurities (e.g., waxes, oils, pectins) to prepare fibers for further processing. | Essential for dyeing and finishing. |
– Bleaching | Whitens fabric by removing natural colors or stains to provide a uniform base for dyeing. | Ensures even coloration. |
Dyeing | ||
– Coloration | Imparts color to fabrics using various dyes and techniques: | |
– Direct Dyes | Simple dyeing for cellulosic fibers. | Cost-effective and easy to use. |
– Reactive Dyes | Forms strong bonds with cellulosic fibers for excellent colorfastness. | Ideal for vibrant, long-lasting colors. |
– Disperse Dyes | Used for dyeing synthetic fibers like polyester. | Provides deep, even coloration. |
– Pigment Dyes | Uses insoluble pigments dispersed in a binder for vibrant colors. | Often applied to a wide range of fabrics. |
Printing | ||
– Pattern Creation | Applies designs using techniques such as: | |
– Screen Printing | Uses stencils to apply dyes or pigments to fabric. | Suitable for large-scale, simple designs. |
Digital Printing | Employs inkjet technology for intricate designs. | Ideal for detailed and customizable patterns. |
– Fixation | Ensures printed designs adhere to fabric, enhancing durability and colorfastness. | Vital for high-quality prints. |
Finishing and Special Applications
In the final stages of processing, textile chemicals are used to enhance the functionality, durability, and aesthetics of fabrics. These applications ensure the fabric meets specific consumer or industrial needs.
Process | Application | Details |
Finishing | ||
– Fabric Properties | Enhances usability and appearance: | |
– Softening | Makes fabric softer and more comfortable. | Improves hand feel. |
– Wrinkle Resistance | Reduces wrinkling for easier maintenance. | Popular in casual and formal wear. |
– Water Repellency | Protects fabric from water and stains. | Essential for outdoor and technical textiles. |
– Flame Retardancy | Reduces flammability. | Ensures safety in specialized applications. |
– Antimicrobial Treatment | Inhibits bacterial and fungal growth. | Inhibits bacterial and fungal growth. |
Special Applications | ||
– Functional Finishes | Adds unique properties to textiles: | |
– Anti-static | Prevents static electricity buildup. | Prevents static electricity buildup. |
– Conductive | Enables smart textiles with electronic capabilities. | Suitable for wearable technology. |
– Self-cleaning | Repels dirt and stains. | Innovative solution for low-maintenance fabrics. |
Case Study: Successful Textile Chemical Formulation
Challenge: A textile manufacturer faced inefficiencies in cotton dyeing, including long processing times, high energy use, and inconsistent colorfastness.
Solution: Chemists developed a novel dyeing formulation using reactive dyes and a biodegradable, bio-based dye carrier. This enabled low-temperature dyeing, reduced energy consumption, and improved dye uptake and colorfastness.
Results:
- 30% Faster Processing: Increased production capacity.
- Energy Savings: Reduced carbon footprint through low-temperature dyeing.
- Superior Colorfastness: Vibrant, long-lasting colors meeting global standards.
- Sustainability: Bio-based materials and lower energy use enhanced eco-friendliness.
Key Success Factors:
- Collaborative research among experts.
- Focus on sustainability in material selection.
- Rigorous testing and optimization for consistent performance.
This highlights the potential of innovative formulations to improve efficiency, sustainability, and product quality in textile manufacturing.
The Formulation of Textile Chemicals Flowchart guides the development of effective and sustainable textile products. Key steps include:
- Needs assessment: Define desired fabric properties.
- Ingredient selection: Choose safe, eco-friendly chemicals.
- Formulation development: Create and optimize chemical mixtures.
- Testing: Conduct rigorous lab and pilot-scale tests.
- Production: Scale-up, implement quality control, and ensure safety.
- Continuous improvement: Refine processes for better performance and sustainability.
This systematic approach prioritizes innovation, sustainability, and collaboration to meet industry demands while minimizing environmental impact.
Read more: Global Textile Chemicals Business: A Comprehensive Overview