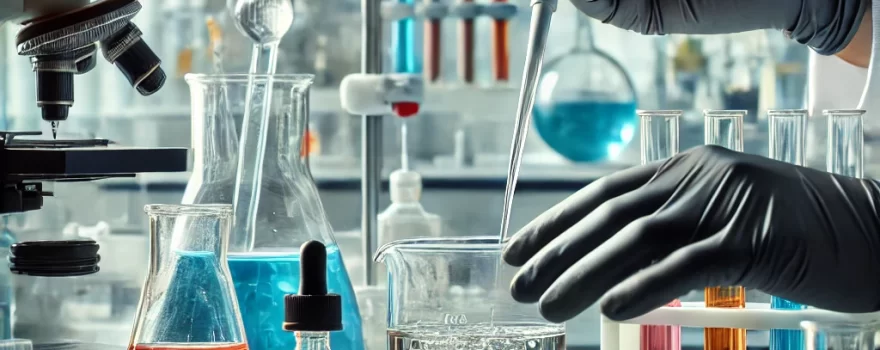
Table of Contents
The development of enhanced fabric properties is fundamentally linked to the formulation of textile chemicals flowchart. This structured process delineates the transformation of raw materials into precisely engineered textile finishes. The procedure extends beyond simple ingredient mixing; it demands a thorough comprehension of chemical interactions, substrate behavior, and operational parameters. Precision is indispensable. This methodology establishes the foundational framework for textile refinement. Each sequential step and decision is of critical importance. This document elucidates the conversion of raw materials into solutions that impart specific characteristics such as stain resistance, fabric softening, and color enhancement.
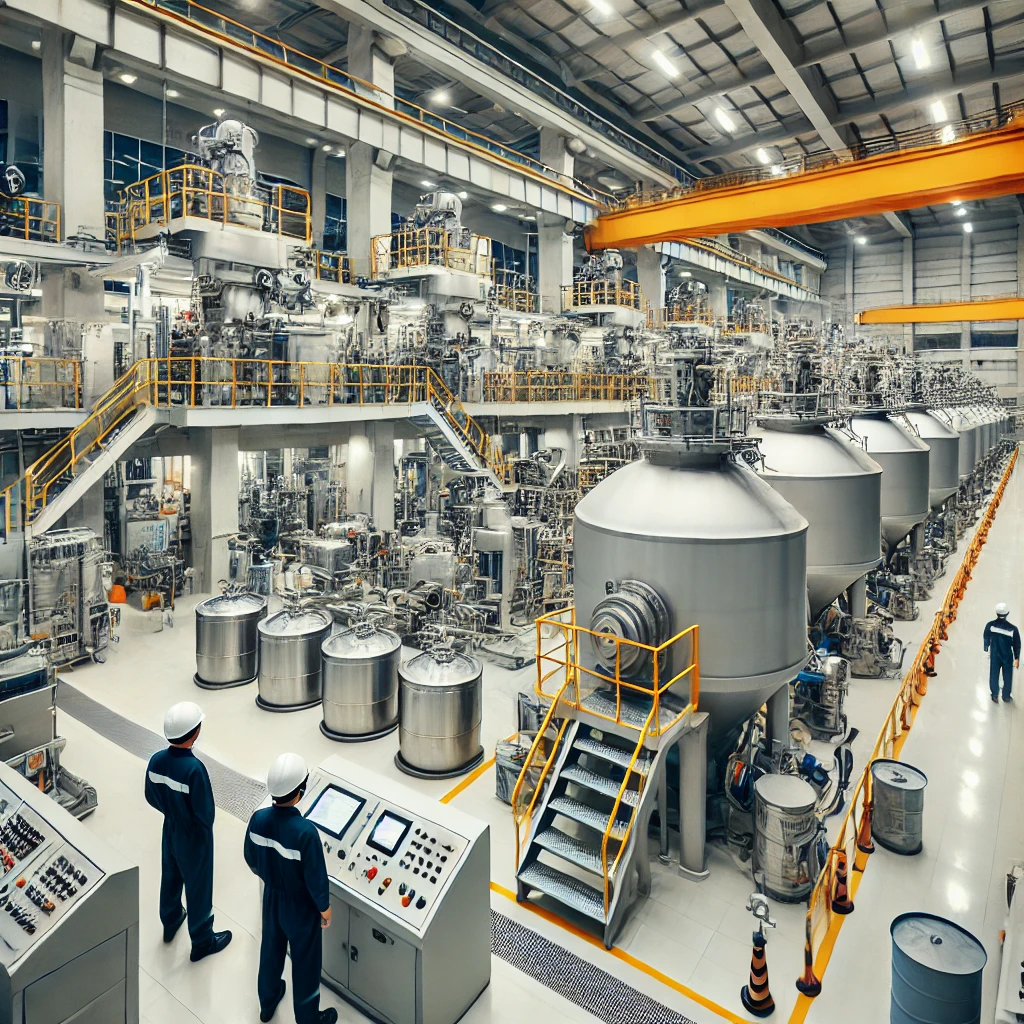
Formulation of Textile Chemicals Flowchart
The composition of textile chemical formulations comprises several essential elements that contribute to fabric performance. These components are delineated as follows:
Active Ingredients: These constituents provide the core functionality, including water repellency, flame resistance, and color modification.
Solvents: These are the carriers, the mediums in which the active ingredients dissolve. They make it possible to apply the chemicals evenly to the fabric. Water, alcohols, and other organic solvents are common choices.
Surfactants: These are the mediators, reducing surface tension and helping the active ingredients penetrate the fabric. They ensure that the chemicals adhere properly.
Additives: This is where the fine-tuning happens. Additives can include:
Stabilizers: They prevent the chemicals from degrading over time.
pH Adjusters: They maintain the acidity or alkalinity of the formulation.
Defoamers: They prevent excessive foaming during application.
Thickeners: They adjust the viscosity of the formulation.
Binders: these are the components that help the active ingredients to adhere to the textile fibers.
Each component plays a crucial role, and the right balance is key. How do we know which ones to use, and in what quantities? That’s where the formulation of textile chemicals flowchart comes in. It guides us through the selection and combination of these essential elements.
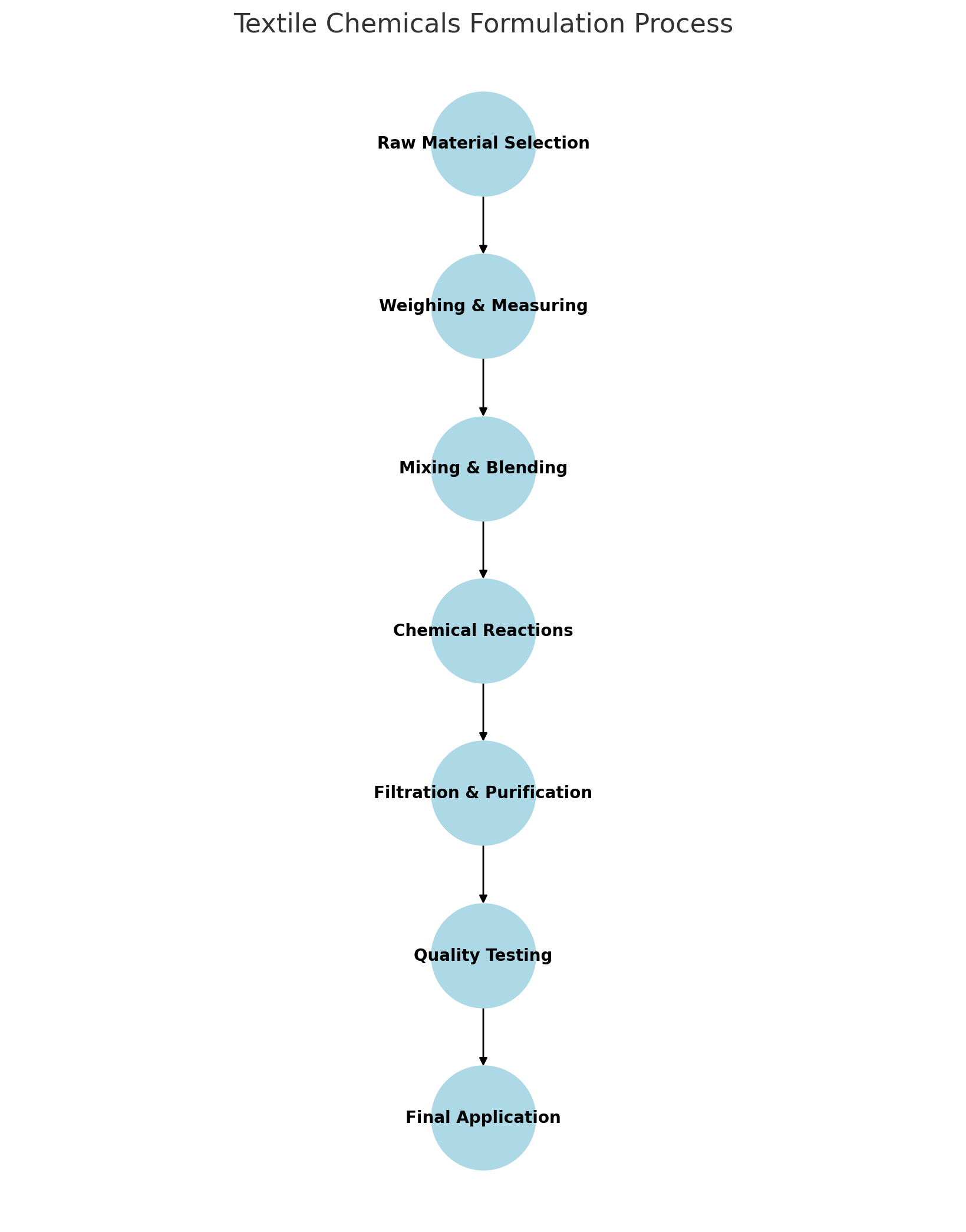
Key Steps
The formulation of textile chemicals flowchart comprises a series of sequential steps:
- Needs Assessment:
Before any laboratory work begins, a detailed understanding of the end-use requirements is necessary. This step, crucial to the formulation of textile chemicals flowchart, dictates the specific chemical properties needed to achieve the desired outcome.
- First, what problem are we solving? Do we need a water repellent? A softer finish? This defines the desired properties.
- What are the specific requirements of the fabric?
- What are the end use requirements?
- Ingredient Selection:
What is the cost of raw materials?
- Laboratory Formulation:
- Small-scale testing is crucial. We mix the ingredients in precise ratios and test the resulting formulation.
- Does the formulation meet the required specifications?
- What are the stability characteristics of the formulation?
- Pilot Testing:
- If the lab results are promising, we move to pilot-scale testing. This involves applying the formulation to larger fabric samples.
- How does the formulation perform under simulated production conditions?
- Are there any scale-up issues?
- Production Formulation:
How can we maintain quality control?
Once we have a successful pilot, we scale up to full production. This involves optimizing the process for large-scale manufacturing.
What are the optimal production parameters?
Based on the needs, we choose the active ingredients, solvents, surfactants, and additives.
What raw materials are available?
- Quality Control:
Are there any deviations from the target properties?
Consistent and thorough quality assessments are performed during each phase of the formulation of textile chemicals flowchart. This includes testing for consistency, stability, and performance.
Does the final product meet all specifications?
- Application and Evaluation:
Does the finished textile meet the end use requirements?
The formulated chemical is applied to the textile.
The finished textile is evaluated for performance.
This iterative process permits adjustments and enhancements at each stage. That’s where the formulation of textile chemicals flowchart comes in. It guides us through the selection and combination of these essential elements.
Raw Material Selection and Mixing
The selection and mixing of raw materials are critical stages of the formulation of textile chemicals flowchart.
Selection Criteria:
Purity: We need raw materials with high purity levels. Impurities can mess with the final product.
Consistency: Batch-to-batch consistency is vital. Variations can lead to unpredictable results.
Compatibility: The chosen materials must play well together. Chemical disputes are prohibited.
Cost-effectiveness: Striking a balance between performance and cost presents an ongoing challenge.
Availability: Can the raw materials be sourced reliably?
Mixing Techniques:
Order of Addition: The sequence in which ingredients are added matters. Some chemicals react violently if mixed in the wrong order.
Mixing Speed and Time: These parameters affect the homogeneity of the mixture. Too fast or too long can cause degradation.
Temperature Control: Many reactions are temperature-sensitive. We need to maintain precise temperature control.
Agitation: Proper agitation is required to achieve a homogenous mixture.
Quality Checks:
Incoming Material Inspection: Every batch of raw materials undergoes a thorough examination to ensure quality and purity.
In-Process Checks: Samples are taken during mixing to ensure the formulation is on track.
Viscosity checks: The thickness of the solution is measured.
pH checks: The acidity or alkalinity is measured.
These procedures are essential for achieving a homogenous and efficacious formulation. This phase establishes the foundation for the subsequent development of the formulation of textile chemicals flowchart.
Chemical Reactions and Stability Control
The regulation of chemical reactions and the maintenance of formulation stability are crucial. Its one of the most important steps of formulation of textile chemicals flowchart
Understanding Reactions:
We need to know the specific reactions that will occur. Will it be an acid-base reaction? An oxidation-reduction?
What are the kinetics of the reactions? How fast will they proceed?
Are there any unwanted side reactions? We need to minimize these.
Stability Control:
Shelf Life: How long will the formulation remain stable? We need to prevent degradation.
Temperature Stability: Will the formulation withstand temperature fluctuations?
pH Stability: Maintaining the correct pH is critical for many formulations.
Viscosity Stability: Changes in viscosity can effect application.
Sedimentation control: preventing the chemicals from settling.
Control Measures:
Inhibitors: These are added to slow down or prevent unwanted reactions.
Stabilizers: These enhance the shelf life and prevent degradation.
pH Buffers: These maintain the desired pH range.
Temperature regulation: Keeping the chemical at the desired temperature during storage and production.
Proper storage: storing the chemicals in the correct containers, and conditions.
These measures ensure the predictable behavior of the formulation, thus advancing the spirit of using formulation of textile chemicals flowchart for optimum eresults.
Filtration, Testing, and Final Processing
We’re nearing the finish line! After the reactions are controlled and the mixture is stable, it’s time for filtration, rigorous testing, and the final processing steps of the formulation of textile chemicals flowchart. This is where we polish our product to perfection.
Filtration:
Why filter? To remove any unwanted particles or impurities. This ensures a clean, consistent product, and thus a successful adherence to the formulation of textile chemicals flowchart.
What type of filtration? It depends on the formulation. We might use membrane filtration, depth filtration, or other techniques.
What size particles are we targeting? This determines the filter pore size.
Testing:
What tests are essential?
Viscosity: Is it within the required range?
pH: Is the acidity or alkalinity correct?
Concentration: Are the active ingredients at the desired levels?
Stability: Does it hold up under various conditions?
Performance testing: Does the chemical perform as intended on the textile?
How often do we test? Throughout the process, and on the final product.
What standards do we follow? Industry standards and internal specifications
Final Processing:
Packaging: How do we package the product? It must be safe and suitable for storage and transport.
Labeling: Accurate labeling is crucial for safety and compliance.
Storage: Proper storage conditions are essential to maintain product quality.
Dilution: Some chemicals are sold as concentrates, and require dilution before application.
Quality checks: Final quality checks before shipping.
These procedures ensure the product’s readiness for application. It’s the culmination of all the previous steps in the formulation of textile chemicals flowchart.
Types of Textile Chemicals
Dyes and Pigments:
These provide color to textiles.
Dyes dissolve in water, while pigments are insoluble.
Applications: Coloring fabrics, yarns, and fibers.
Finishing Agents:
These enhance the performance and aesthetics of textiles.
Types:
Softening agents: Improve fabric feel.
Water repellents: Make fabrics water-resistant.
Flame retardants: Reduce flammability.
Wrinkle-free finishes: Minimize creasing.
Antimicrobial finishes: prevent the growth of bacteria.
Applications: Apparel, home textiles, and industrial fabrics.
Sizing Agents:
These strengthen yarns for weaving.
They add temporary stiffness and strength.
Applications: Weaving processes.
Printing Chemicals:
These are used in textile printing.
Types: Thickeners, binders, and fixing agents.
Applications: Fabric printing.
Auxiliary Chemicals:
These support various textile processes.
Types: Surfactants, emulsifiers, and dispersants.
Applications: Wet processing of textiles.
Pretreatment Chemicals:
These chemicals prepare the textile for further processing.
Types: Desizing agents, scouring agents, bleaching agents.
Applications: Cleaning and preparing textiles for dyeing and finishing.
Each type of chemical has a specific function, and the right selection is crucial for achieving the desired textile properties. All these successful categorisations came about due to proper implementation of the formulation of textile chemicals flowchart process.
Sustainable Approach
The textile industry is waking up to its environmental impact. It’s time to talk about greener chemistry. How can we formulate textile chemicals that are less harmful to the planet? Implementation of formulation of textile chemicals flowchart itself can lead to eureka moments of realisation in this regard.
Replacing Hazardous Chemicals:
Traditional formulations often use harsh chemicals. We’re looking for safer alternatives.
Bio-based chemicals: These are derived from renewable resources.
Less toxic chemicals: Chemicals that break down easily in the environment.
Reducing Water and Energy Consumption:
Formulations that require less water and energy are a win-win.
Low-temperature processes: These reduce energy usage.
Concentrated formulations: These minimize water usage.
Minimizing Waste:
We can’t eliminate waste entirely, but we can minimize it.
Closed-loop systems: These recycle water and chemicals.
Formulations that produce less by-products.
Developing Biodegradable Chemicals:
Chemicals that break down naturally are less likely to pollute.
Natural polymers: These are biodegradable and sustainable.
Enzyme-based formulations: These use natural catalysts.
Life Cycle Assessment:
Evaluating the environmental impact of a chemical from cradle to grave.
This helps identify areas for improvement.
It helps choose the most sustainable options.
Implementing Green Chemistry Principles:
Designing chemical products and processes that reduce or eliminate hazardous substances.
Prevention: It is better to prevent waste than to treat or clean up waste after it has been created.
Atom Economy: Synthetic methods should be designed to maximize the incorporation of all materials used in the process into the final product.
We’re shifting our focus. It’s not just about performance anymore; it’s about responsibility.
Future Trends
Where are we headed? The textile industry is on the cusp of some exciting changes, and chemical formulation is right at the heart of it. Let’s peek into the crystal ball and see what’s coming.
Smart Textiles:
Think fabrics that can monitor your health, change color, or even generate energy.
Chemical formulations will play a key role in enabling these functionalities.
Conductive inks, responsive polymers, and sensor coatings are just a few examples.
Nanotechnology:
Using nanoparticles to enhance textile properties.
This allows for precise control over performance, such as improved durability, UV protection, and self-cleaning.
This means chemicals that work on a molecular level.
Personalized Textiles:
Imagine fabrics that are customized to your specific needs and preferences.
On-demand chemical treatments and digital printing will make this possible.
This will change how we think of fabric creation.
Circular Economy:
Textiles designed for recycling and reuse.
Chemical formulations that support closed-loop systems.
This will reduce waste and minimize environmental impact.
Advanced Bio-based Chemicals:
Increased reliance on sustainable, renewable resources.
Enzyme-based processes and bio-inspired materials.
This will lead to more eco-friendly textiles.
Automation and AI:
Automated formulation and testing.
AI-driven optimization of chemical processes.
This will enhance both efficiency and consistency.
Conclusion
The future of textile chemistry is about innovation, sustainability, and personalization. We’re moving towards a world where fabrics are smarter, greener, and more tailored to our individual needs. The formulation of textile chemicals flowchart will continue to evolve, adapting to these new demands.
Also Read: Textile Chemicals: The Secret Sauce Behind Your Clothes