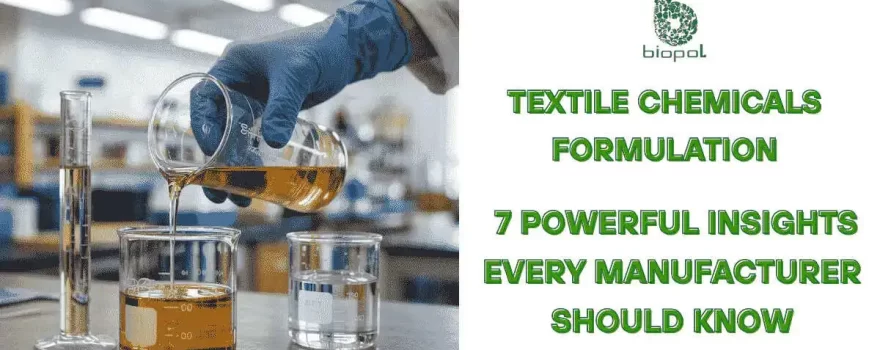
Textile Chemicals Formulation is a combination of chemicals that plays a crucial and specific role in modern fabric manufacturing. It creates specific properties on a fabric according to its preparation. These formulations help impart superior durability, enhanced aesthetics, and specialized functionalities in fabrics. Developing effective formulations requires a precise balance of science, innovation, and sustainability. This article explores essential guidelines and best practices for creating textile chemical formulations that meet industry standards and environmental regulations.
Table of Contents
What is a Textile Chemicals Formulation?
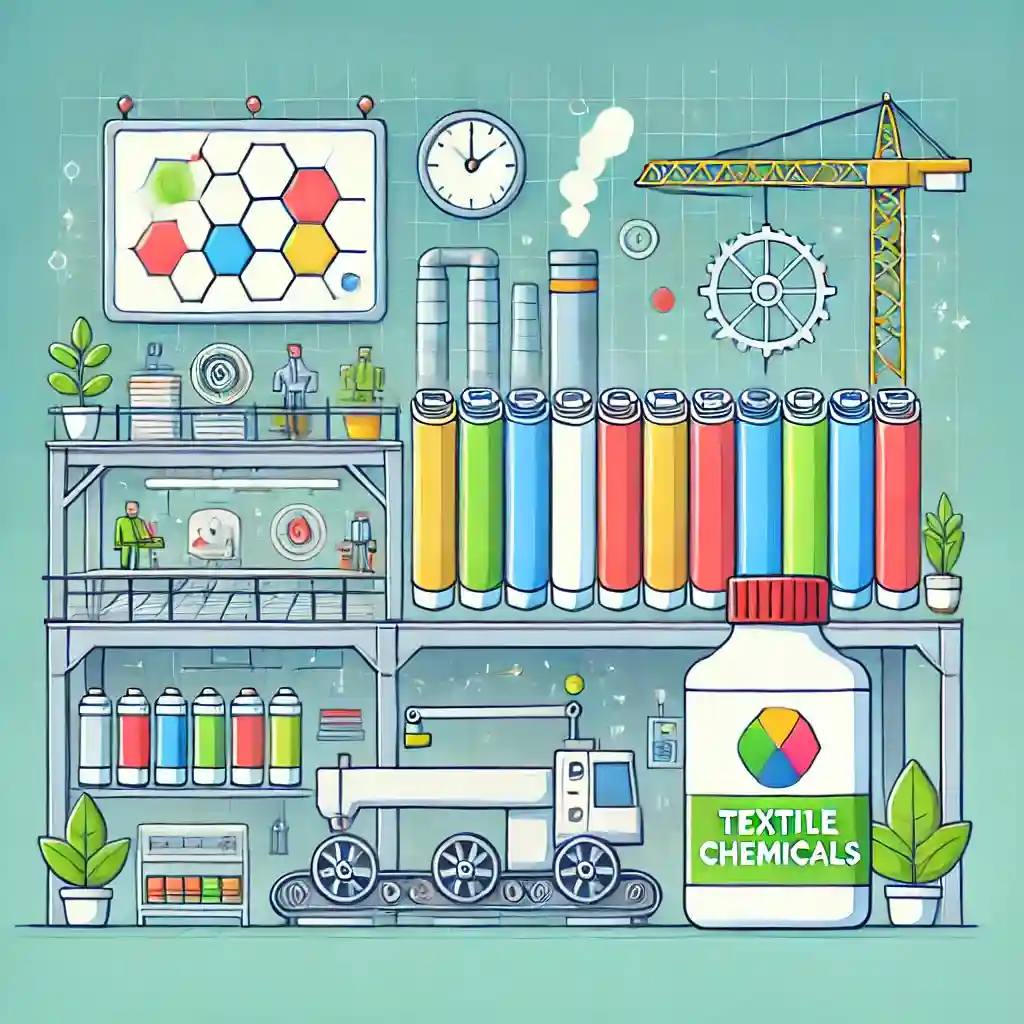
Mixing textile chemicals in the right proportion to achieve a specific target of imparting a specific quality to any fabric is what makes a textile chemicals formulation. There are many types of formulations, viz. wetting agents, levelling agents, sizing agents, enzymes, softeners etc. Each serves a specific purpose and function.
Principles for Developing Formulations
- Purpose-Driven Formulation
Define the specific goal of the chemical—whether it’s enhancing durability, improving texture, or imparting advanced properties like UV resistance or stain repellency.
- Fabric Compatibility
Consider the fabric type (natural or synthetic fibers) and structure (woven or nonwoven). Compatibility ensures performance without compromising fabric integrity.
- Regulatory Compliance
Adhere to international standards such as REACH, ZDHC, and Oeko-Tex, which govern ingredient safety, environmental impact, and waste management.
- Sustainability and Cost Efficiency
Aim for formulations that balance functionality and cost while minimizing environmental impact. Bio-based ingredients and green chemistry are emerging as sustainable alternatives.
Categories of Formulations and Their Functions
Category | Function | Examples |
Pre-treatment Chemicals | Prepare fabrics by removing impurities, improving fabric texture for further processing. | Scouring Agents, Desizing Agents |
Dyeing and Printing Chemicals | Ensure vibrant and uniform color application, enhancing visual appeal and fabric quality. | Fixatives, Leveling Agents |
Finishing Chemicals | Ensure vibrant and uniform color application, enhancing visual appeal and fabric quality. | Fixatives, Leveling Agents |
Specialty Chemicals | Provide advanced functionalities for specific textile applications, such as durability and resistance. | UV Resistance, Flame Retardancy Coatings |
For better clarity on how to go about making great chemical formulations, read our detailed blog on Formulation Guidelines for Textile Chemicals.
Processes in Creating Formulations
Process | Description | Key Considerations |
Needs Assessment and Target Definition | Clearly define specific requirements and desired outcomes for the textile chemical. | – Type of fabric – Intended application (e.g., dyeing, finishing, printing) – Desired performance (e.g., colorfastness, water repellency) |
Ingredient Selection and Sourcing | Select appropriate raw materials based on functionality, compatibility, and environmental impact. | – Synthetic vs. natural-based chemicals – Cost and availability – Regulatory compliance |
Formulation Development and Optimization | Experiment with ingredient combinations and parameters to achieve desired performance through laboratory trials. | Experiment with ingredient combinations and parameters to achieve desired performance through laboratory trials. |
Scale-up and Production | Transition laboratory formulations to production scales while maintaining consistency and quality. | – Quality control across batches – Robust production protocols |
Performance Evaluation and Testing | Rigorously test the final product to ensure it meets defined requirements and gather feedback for improvement. | – Colorfastness and durability – Environmental impact – End-user feedback |
By following these structured processes, the formulation of textile chemicals ensures effective processing, meets market demands, minimizes environmental impact, and guarantees safety and performance. We have further summarised the process in a beautiful flowchart for you to read at our detailed blog about the Formulation of Textile Chemicals Flowchart.
Choosing the Right Raw Materials
Choosing the right raw materials is a critical step in the Formulation of Textile Chemicals Flowchart. The performance and sustainability of the final product heavily rely on the quality and characteristics of the ingredients used.
Category | Key Considerations |
Performance | – Select materials with desired functional properties (e.g., dyeing ability, wetting, dispersing). – Ensure compatibility with other formulation ingredients. – Assess impact on final fabric properties |
Sustainability | – Use renewable and biodegradable materials when possible. – Avoid hazardous chemicals, opting for safer alternatives. – Evaluate environmental impact during sourcing and production. |
Economic | – Prioritize cost-effective raw materials. – Ensure availability and mitigate risks of price fluctuations. – Partner with reliable and ethical suppliers. |
Regulatory Compliance | – Adhere to relevant environmental and safety regulations. – Stay updated on industry standards and best practices. |
Preliminary Testing and Adjustments
Key Aspects of Preliminary Testing
- Compatibility Testing:
- Check chemical interactions: precipitation, color changes, gas evolution.
- Assess fabric compatibility: dye uptake, fabric damage, residual chemicals.
- Performance Evaluation:
- Conduct small-scale trials for:
- Colorfastness: Resistance to washing and light.
- Durability: Performance after repeated washing/dry cleaning.
- Sensory Properties: Hand feel, drape, and texture.
- Conduct small-scale trials for:
- Stability Testing:
- Evaluate storage stability under varying conditions (temperature, humidity).
- Determine shelf life for safety and effectiveness.
Adjustment
- This ensures textile chemicals are effective, safe, and aligned with desired performance goals.
- Modify ingredients to address compatibility or performance issues.
- Optimize processing parameters (e.g., temperature, time, pH).
- Add auxiliary agents for improved stability and efficacy.
Pilot Batch Testing: Optimizing Formulations
Pilot batch testing is a crucial step in the Formulation of Textile Chemicals Flowchart. It bridges the gap between small-scale laboratory trials and full-scale production, allowing us to:
Key Aspect | Key Aspect | Purpose |
Validate Laboratory Findings | Confirm that formulations developed in the lab perform effectively on a larger scale. | Ensure scalability and performance consistency. |
Identify and Address Potential Issues | ||
– Scale-Up Challenges | Address issues like mixing, heating, and cooling at larger volumes. | Prevent inefficiencies and maintain quality. |
– Equipment Limitations | Identify and adapt to production equipment constraints. | Ensure compatibility between formulation and machinery. |
– Consistency Issues | Test the reproducibility of the formulation at scale. | Guarantee uniform product quality across batches. |
Scale-Up Considerations | ||
– Equipment Selection | Choose appropriate equipment for mixing, heating, and other steps based on formulation properties. | Ensure efficient and accurate processing. |
– Process Control | Implement robust controls for critical parameters like temperature and mixing. | Achieve consistent results in production. |
– Material Handling | Develop safe and efficient procedures for handling large volumes of chemicals. | Minimize risks and streamline workflow. |
Performance Evaluation | ||
– Thorough Testing | Conduct comprehensive tests for colorfastness, durability, sensory properties, and environmental impact. | Verify that the pilot batch meets quality standards. |
– Comparison with Lab Results | Compare pilot batch performance to laboratory outcomes. | Ensure alignment with initial expectations. |
Data Analysis and Optimization | ||
– Analyze Data | Collect and analyze data to identify areas for improvement. | Refine formulations and processes for better outcomes. |
– Process Optimization | Adjust formulations, parameters, or equipment to enhance performance and efficiency. | Resolve issues and achieve optimal results. |
– Document Findings | Record all insights and observations from the pilot testing phase. | Provide a reference for full-scale production and future use. |
Optimization Techniques
Design of Experiments (DoE):
- Structured approach to test multiple variables (e.g., ingredients, parameters) efficiently.
- Minimizes experiments while maximizing insights.
- Statistical analysis identifies significant factors for optimal results.
Response Surface Methodology (RSM):
- Develops mathematical models to link inputs (e.g., formulations, conditions) with outcomes (e.g., durability, colorfastness).
- Predicts optimal combinations of variables.
- Visualizes relationships through response surface plots.
Artificial Intelligence (AI) and Machine Learning:
- Builds predictive models for formulation performance.
- Uses historical and experimental data for data-driven optimization.
- Continuously refines models for improved outcomes over time.
Evolutionary Algorithms:
- Mimics natural selection to find the best solutions.
- Handles complex problems with multiple variables and constraints.
- Robust against noisy or uncertain data.
Finalizing the Formulation
The final stage of the Formulation of Textile Chemicals Flowchart involves transitioning from successful pilot batches to full-scale production. This requires meticulous attention to detail and a robust quality control system.
Aspect | Details | Purpose |
1. Production Scale-Up | ||
– Equipment and Process Validation | Ensure production equipment and processes meet formulation specifications. | Guarantee consistent and reliable production. |
– Capacity Planning | Determine production capacity to meet market demand. | Avoid delays and shortages. |
– Raw Material Sourcing | Secure reliable and consistent sources of high-quality raw materials. | Maintain consistent input quality for production. |
2. Quality Control and Assurance | ||
– Comprehensive QC Plan | Implement quality checks at all stages: | |
– Incoming Raw Material Inspection | – Incoming Raw Material Inspection | Prevent defective inputs from affecting production. |
– In-Process Control | Monitor critical parameters (e.g., temperature, pH, mixing time). | Monitor critical parameters (e.g., temperature, pH, mixing time). |
– Finished Product Testing | Conduct thorough tests on finished products to meet standards. | Deliver high-quality, compliant products. |
Documentation | Record raw material usage, process parameters, and test results. | Ensure traceability and accountability. |
3. Safety and Environmental Compliance | ||
– Safety Protocols | Implement measures to protect workers from chemical hazards. | Ensure workplace safety and minimize health risks. |
– Environmental Management | Apply waste reduction, recycling, and eco-friendly practices. | Reduce environmental footprint and promote sustainability. |
– Regulatory Compliance | Adhere to all relevant environmental and safety regulations. | Avoid legal issues and maintain ethical standards. |
4. Cost Optimization | ||
– Continuous Improvement | Monitor and refine production processes to enhance efficiency. | Reduce operational costs while maintaining quality. |
– Supply Chain Management | Optimize supply chain to minimize costs and ensure timely material delivery. | Ensure cost-effective and uninterrupted production. |
By carefully addressing these considerations, we can successfully transition the finalized textile chemical formulation to full-scale production, ensuring consistent quality, safety, and environmental sustainability
Quality Control Measures
Ensuring quality control in textile chemical formulation is essential to guarantee consistent performance, safety, and adherence to standards throughout the production process. Below are key quality control practices restructured for clarity:
Raw Material Quality Checks
- Visual Inspection: Detect contamination, discoloration, or physical irregularities in raw materials.
- Chemical Verification: Conduct detailed tests to confirm material composition and purity:
- Titration: Measure concentrations of reactive substances like acids or bases.
- Spectrophotometry: Analyze the light absorbance of specific compounds.
- Chromatography: Separate and examine components in a mixture.
- Supplier Compliance: Periodically audit suppliers to verify adherence to quality and safety protocols.
Process Monitoring and In-Process Testing
- Critical Parameter Tracking: Continuously oversee essential factors such as:
- Temperature: Maintain precise control during heating, mixing, or cooling stages.
- pH Levels: Adjust pH to ensure reaction stability and effectiveness.
- Mixing Conditions: Verify uniformity through consistent mixing times and speeds.
- Sample Testing: Evaluate samples at intermediate stages for quality and consistency.
Finished Product Evaluation
- Performance Assessment: Verify the end product meets required specifications:
- Colorfastness: Test resistance to washing, light exposure, and wear.
- Durability: Check finishes like water repellency, flame retardancy, or wrinkle resistance.
- Fabric Properties: Assess the feel, drape, and tactile quality of treated materials.
- Chemical Safety Tests: Screen for harmful residues like heavy metals or hazardous substances.
- Stability Analysis: Store finished products under controlled conditions to observe long-term performance and safety.
Documentation and Standardization
- Detailed Record Maintenance: Document every step of the production process, including:
- Material specifications and test results.
- Production parameters and adjustments.
- Final product performance data.
- Quality Frameworks: Adhere to established standards like ISO 9001 to promote consistency and continuous quality improvement.
Commitment to Continuous Improvement
- Data Utilization: Regularly review quality control metrics to spot inefficiencies or trends.
- Issue Resolution: Investigate quality deviations using root cause analysis and implement corrective actions.
- System Upgrades: Periodically evaluate and enhance the overall quality management system to align with evolving standards and market needs.
By implementing these quality control measures, manufacturers can produce superior textile chemicals that are reliable, sustainable, and tailored to industry demands, while fostering innovation and compliance.
Impact of pH and Temperature
Factor | Impact | Key Considerations |
pH | ||
– Chemical Reactions | Influences ionization and reactivity of chemicals. | Maintain appropriate pH to ensure desired chemical interactions. |
– Dyeing | Affects dye uptake, colorfastness, and fabric appearance. | Adjust pH based on dye type and fabric requirements. |
– Finishing | Impacts the effectiveness of agents like softeners, wrinkle-release agents, and flame retardants. | Optimize pH for each finishing agent to achieve maximum performance. |
– Chemical Stability | Extreme pH values can degrade chemicals, cause precipitation, or lead to undesirable reactions. | Avoid overly acidic or alkaline conditions unless necessary for specific processes. |
– Fiber Compatibility | Specific fibers respond differently to acidic or alkaline conditions. | Match pH of processing bath to the fiber type (e.g., acidic for protein fibers, alkaline for cellulose). |
Temperature | ||
– Reaction Kinetics | Higher temperatures speed up reactions but can cause side reactions or chemical degradation. | Control temperature to balance reaction rates and prevent unwanted effects. |
– Dye Solubility | Increases solubility of dyes, improving uptake and penetration. | Increases solubility of dyes, improving uptake and penetration. |
– Fabric Properties | Impacts shrinkage, crease formation, and hand feel. | Maintain temperature within fabric tolerance levels to preserve quality. |
General Considerations | ||
– Optimal Ranges | Specific pH and temperature ranges vary for each chemical process and desired outcome. | Research and adhere to optimal conditions for each application. |
– Buffer Solutions | Stabilize pH during processing for consistent results. | Incorporate buffers in formulations where necessary. |
– Temperature Control | Accurate temperature management ensures reproducible outcomes and efficiency. | Use reliable temperature regulation systems during production. |
Controlling pH and temperature is crucial in textile chemical formulation to ensure optimal performance, efficient processing, and minimal environmental impact. These factors must be tailored to the specific requirements of each process and fabric type.
Advanced Tools and Techniques
Technology | Description | Impact on Textile Chemical Formulation |
Spectrophotometers | Instruments that measure the absorption of light to analyze chemical properties. | Ensure precise color matching and consistency in formulations. |
Chromatography Systems | Techniques for separating and analyzing chemical components in a mixture. | Enable detailed chemical analysis, ensuring quality and purity. |
Automation | Use of automated systems for mixing and dosing chemicals in formulations. | Improve efficiency, consistency, and scalability in large-scale production. |
Artificial Intelligence (AI) | Machine learning algorithms used to predict formulation outcomes. | Optimize ingredient combinations and enhance formulation accuracy. |
Green Chemistry | Sustainable practices that minimize environmental impact. | Reduce waste, energy consumption, and reliance on harmful chemicals. |
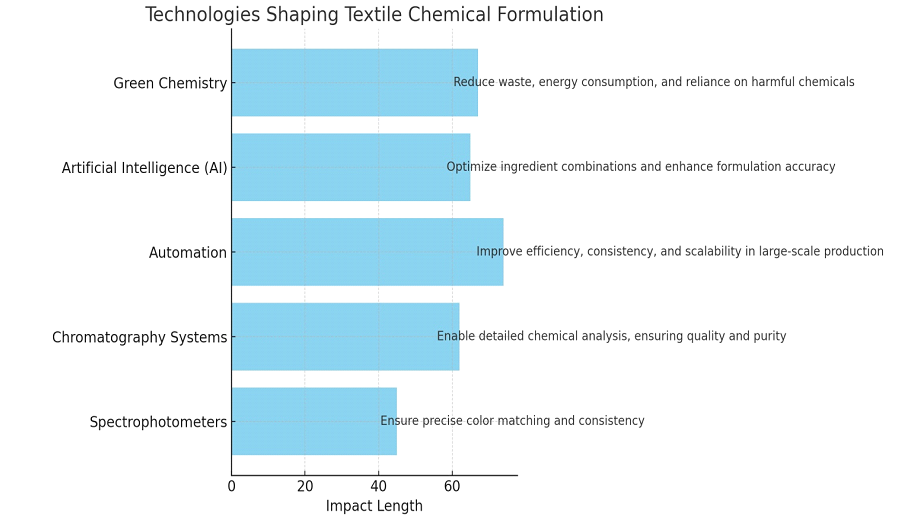
Successful Applications of Formulations
- Apparel Industry: Advanced dyes and softeners enhance fabric aesthetics and comfort.
- Home Textiles: Stain-resistant and water-repellent finishes improve usability and durability.
- Technical Textiles: Specialty chemicals provide functionalities like fire resistance and antimicrobial protection.
Challenges in Textile Chemical Formulations
- Environmental Concerns: Replace toxic substances with biodegradable and bio-based alternatives.
- Performance vs. Cost: Achieve high performance without inflating costs by optimizing ingredient use.
Navigating Global Standards
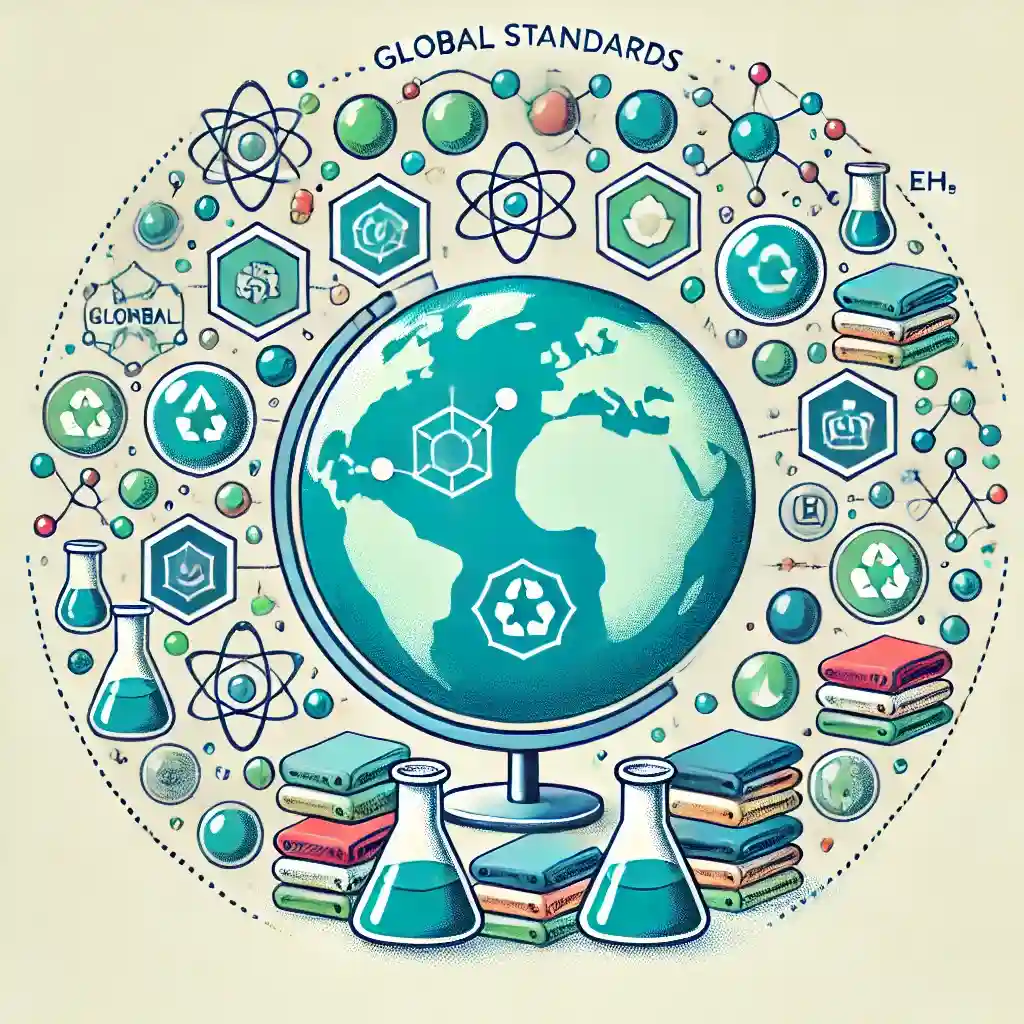
As the textile industry becomes more interconnected globally, navigating regulatory standards for textile chemicals formulation is increasingly complex. Compliance with international regulations, such as REACH (Registration, Evaluation, Authorization, and Restriction of Chemicals), ZDHC (Zero Discharge of Hazardous Chemicals), and Oeko-Tex certification, is essential for ensuring that textile products are safe for consumers and the environment. These regulations govern everything from ingredient safety to waste management, influencing formulation practices and product labeling. This section delves into the key global standards governing textile chemicals, outlining the importance of compliance, the impact on production, and the steps needed to meet these regulations effectively.
Future of Textile Chemicals Formulation
The textile chemical industry is rapidly evolving with groundbreaking innovations, such as:
⦁ Bio-Based Chemicals: Derived from renewable resources to reduce environmental impact.
⦁ Smart Textiles: Chemicals enabling self-healing, temperature regulation, and other advanced functionalities.
⦁ Circular Economy: Formulations that support recycling and fabric reuse.
Best Practices for Textile Chemicals Formulation
Developing textile chemical formulations is a dynamic process requiring scientific knowledge, creativity, and a commitment to sustainability by:
⦁ Understanding fabric properties.
⦁ Selecting eco-friendly ingredients.
⦁ Adhering to global regulations.
⦁ Emphasizing continuous innovation.
FAQs: Textile Chemicals Formulation
What is textile chemicals formulation?
Textile chemicals formulation refers to the precise combination of chemical ingredients—such as surfactants, binders, dyes, and auxiliaries—used to achieve specific effects like dyeing, printing, or finishing in textile processing.
2. Why is formulation important in textile processing?
A well-designed formulation ensures optimal performance, consistent quality, fabric compatibility, and cost-efficiency. It also helps meet environmental and regulatory standards like OEKO-TEX or ZDHC.
3. What factors influence textile chemical formulation?
Key factors include fiber type (natural or synthetic), desired fabric properties (softness, water resistance, colorfastness), processing method (continuous or batch), and end-use application (apparel, technical textiles, home furnishing).
Also Read: Textile Chemicals: The Secret Sauce Behind Your Clothes