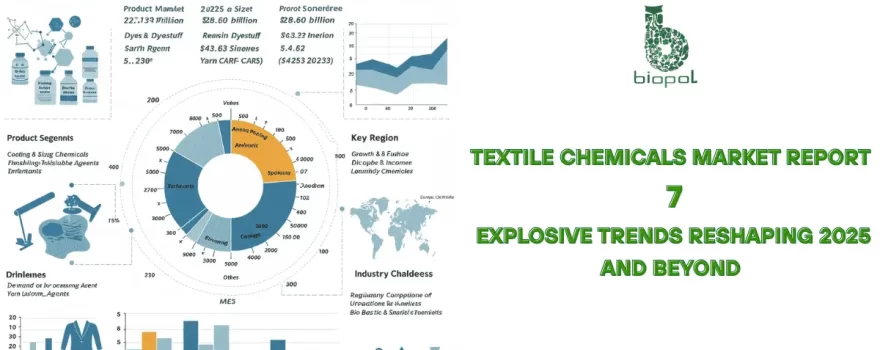
Speciality chemicals uses in textile table printing refer to advanced compounds developed to enhance print accuracy, fabric interaction, and production efficiency. These aren’t everyday ingredients—they’re precision tools that dictate how textiles absorb, hold, and showcase printed designs.
Table of Contents
Specialty chemicals in textile printing are advanced compounds crucial for enhancing print accuracy, fabric interaction, and production efficiency in textile table printing. They are not everyday ingredients but precision tools that dictate how textiles absorb, hold, and showcase printed designs. Their essential role lies in preventing colors from running, patterns from blurring, and ensuring the durability of prints after washing.
Why are they essential?
Without chemical support, textile printing would be chaotic. Specialty chemicals bring order by serving targeted roles throughout the printing process:
- Pre-treatment agents: Clean, soften, and modify the fabric’s surface tension to prepare it for even ink absorption.
- Printing auxiliaries: Adjust ink viscosity, stabilize pigment dispersion, and control print spread for clear and consistent designs.
- Fixation enhancers: Promote strong dye-fiber bonds to ensure long-lasting color and wash resistance.
- Post-treatment agents: Improve fabric feel, boost color fastness, and resist shrinkage or yellowing.
Each chemical class plays a vital part; skipping any can negatively impact the final printed product. They enable consistency at scale across various fabric types like cotton, silk, and synthetics.
Types of Chemicals Used in Table Printing
Speciality chemicals uses in textile table printing involve multiple chemical classes, each serving a critical function. Key types include:
- Pigment binders for adhesion and fastness
- Reactive dyes for bright, wash-resistant prints
- Printing auxiliaries like thickeners, dispersing agents, and wetting agents for control and consistency
Together, these chemicals shape print quality, durability, and fabric behavior. Without the right mix, results fall flat—colors fade, patterns distort, and production stalls.
Role of Chemicals in Each Printing Stage
Specialty chemicals support every stage of textile printing:
- Pre-treatment: Prepare fabric for optimal ink absorption.
- During printing: Thickeners and dispersants maintain design clarity and control ink flow.
- Post-print: Fixation agents lock in color; wash-off chemicals remove residue and enhance fabric feel.
Why Use Specialty Chemicals in Textile Printing?
Their use is critical for achieving high-quality, durable, and visually appealing prints that meet modern standards. They:
- Enhance color fastness, preventing fading.
- Enable precision application, ensuring crisp lines and vibrant patterns.
- Support eco-performance by reducing water usage, waste, and energy consumption.
Applications in Textile Table Printing
Specialty chemicals are used in multiple textile segments:
- Fashion fabrics: Deliver bold prints on cotton, viscose, and blends.
- Upholstery printing: Ensure deeper penetration and high rub resistance for durability.
- Home textiles (curtains, bed linen): Enhance washability and brightness.
How to Select the Right Chemicals
Effective selection requires consideration of:
- Fabric type: Different fabrics (cotton, polyester, blends) need specific formulations.
- Printing method: Screen, rotary, or digital printing have unique chemical requirements.
- Fixation process: Heat, steam, or UV fixation affects chemical compatibility.
- Print recipe: Viscosity and drying time must align with chosen chemicals.
- Supplier quality: Certified suppliers reduce the risk of inconsistent batches.
Eco-Friendly Alternatives
The textile industry increasingly adopts sustainable specialty textile chemicals and solutions:
- Low-VOC chemicals: Reduce harmful emissions and improve workplace safety.
- Green textile processes: Minimize water and energy use.
- Biodegradable additives: Naturally break down, reducing landfill waste.
- Regulatory compliance: Align with environmental standards.
Finding the Right Chemical Supplier
Choosing a trusted supplier ensures quality and smooth production:
- Experience: Suppliers familiar with textile printing needs.
- Compliance certification: Verified adherence to environmental and safety standards.
- Product quality and consistency: Sample testing and batch uniformity.
- Technical support: Guidance and troubleshooting assistance.
- Supply chain reliability: Timely delivery to prevent delays.
FAQs on Speciality Chemicals for Textile Printing
What are some of the chemicals used in textile processing?
Mordants, dyes, bleaching agents, softeners, and fixatives are commonly used in textile processing.
Which chemical is used for color fixing?
Fixation agents like reactive dyes or polyfunctional fixatives are used for color fixing.
Which chemical is used in fabric?
Sizing agents, softeners, and finishing chemicals are applied to fabrics.
Which chemical is used in textile design printing?
Pigment binders, printing auxiliaries, and reactive dyes are used in textile printing.